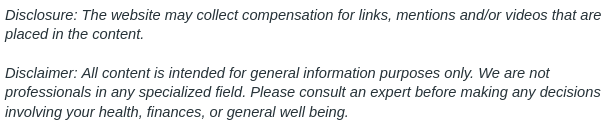
- Digital CMMS enhances scheduling efficiency, facilitating the seamless implementation of preventative maintenance plans.
- Proper training for maintenance staff is crucial for early problem detection and effective equipment upkeep.
- Analyzing maintenance data helps identify failure patterns, enabling continuous operational improvements and resource optimization.
- Proactive maintenance strategies transition industries from reactive repairs to preventive care, enhancing safety and reducing costs.
Preventive maintenance refers to the routine upkeep and repairs of equipment before faults become serious problems, aiming to prolong the life of the equipment and ensure its efficient operation. This proactive approach helps avoid unexpected downtime and significantly reduces the costs associated with major repairs. It’s a crucial strategy applicable across various industries, from manufacturing to information technology.
Core Principles and Activities

At its heart, preventative maintenance is a proactive strategy. The following are activities performed to ensure that problems are addressed before they arise.
Regular Cleaning
Regular cleaning is crucial to preventive maintenance, ensuring equipment is free from dust, dirt, and grime that can negatively impact performance. In large industries, versatile pipeline pigs ensure the smooth delivery of fluids they need. Keeping these types of equipment clean makes inspecting for and addressing minor problems easier before they escalate.
Routine Inspections
Along with regular cleaning, routine inspections are integral to preventive maintenance, serving as a defense against potential equipment failure. During these inspections, technicians examine equipment for signs of wear, corrosion, leaks, and other indicators of potential issues. This systematic examination helps identify small problems before they escalate into costly repairs.
Adjusting Installations
Adjusting installations is another critical aspect of preventive maintenance. This process involves making minor adjustments to equipment to ensure it operates within its intended parameters.
Such adjustments include aligning belts, tightening loose components, recalibrating instruments, and updating software settings. These small parts contribute greatly to the large functions of certain equipment.
Component Part Replacement
Part replacement involves periodically inspecting and replacing worn or outdated parts before they fail. Employing a proactive approach to component replacement safeguards against unexpected downtime and optimizes the efficiency of the equipment. Some components must be replaced in the long run, so a good inspection strategy should be partnered with them.
Benefits of a Proactive PM Program
With some of the strategies given, your company or establishment should be guaranteed to have the following:
Increased Equipment Lifespan
A careful approach to machinery provides a healthy lifestyle for your equipment, ensuring it’s set for the long run. Identifying and solving problems early minimizes wear and tear, and potential overloads are averted. Regular, scheduled maintenance addresses current issues and includes tasks like lubrication and filter changes that prevent future complications.
Improved Operational Efficiency
Equipment that is in top condition operates at its designed capacity. Production translates into consistent output when machines do what they’re meant to without hiccups. Ensuring that equipment is efficient also means that companies aren’t overcompensating for lost capabilities, such as repairs or bottleneck identification.
Reduced Maintenance Costs
While these measures require an initial investment, the overall cost-savings are compelling. By identifying and addressing issues early, the need for costly emergency repairs is greatly reduced. Preventative maintenance allows companies to keep maintenance costs predictable and manageable by phasing out old parts that could lead to system failure well before they do.
Enhanced Safety Standards
We can’t discuss PM’s value without broaching the safety subject. A well-executed PM program is integral to maintaining a safe working environment. Regular inspections can identify worn components, equipment malfunctions, or potential hazards that could lead to accidents. By systematically inspecting and maintaining equipment, companies demonstrate a commitment to the well-being of their workforce.
Best Practices for Implementing a Preventative Maintainance
Develop a PM Schedule
A PM schedule should be business-specific. Equipment that is housed in one industry operates differently compared to others. The environment in which it is placed is also a factor when planning. Knowing these factors makes a maintenance plan effective for the personnel that will implement them and the product or service it will produce.
Utilize Technology for PM Management
After the planning phase, there should be a monitoring mechanism that checks the efficiency of the produced schedule. Ease of implementation can be augmented by digital technology such as different CMMS (Computerized Maintenance Management Systems)
Train and Empower Maintenance Staff
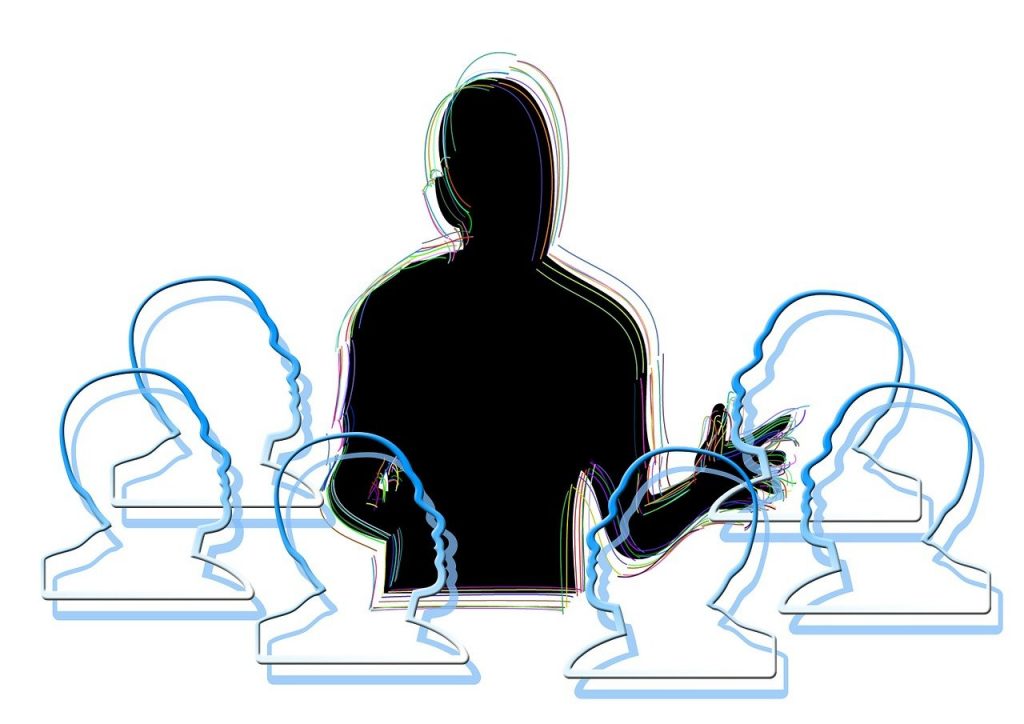
The importance of proper training for technicians cannot be overstated when seeking to ensure the effectiveness of PM procedures. A well-trained maintenance staff is more equipped to identify potential issues before they become critical failures, perform accurate repairs, and optimally maintain equipment to prevent unnecessary downtime.
Data Analysis and Continuous Improvement
By meticulously examining repair records, maintenance logs, and equipment performance data, organizations can identify recurring issues and understand the root causes of breakdowns. Ultimately, leveraging PM data for continuous improvement leads to more efficient use of maintenance resources.
Preventative maintenance serves as a cornerstone strategy for large industries aiming to maximize equipment lifespan, operational efficiency, and safety standards, all while minimizing maintenance costs. This transitions industries from reactive repairs to proactive upkeep, preventing minor issues from snowballing into significant disruptions. Furthermore, proactive maintenance fosters a safer work environment for workers.